What is the most common injury caused by working with Machines Unsafely?
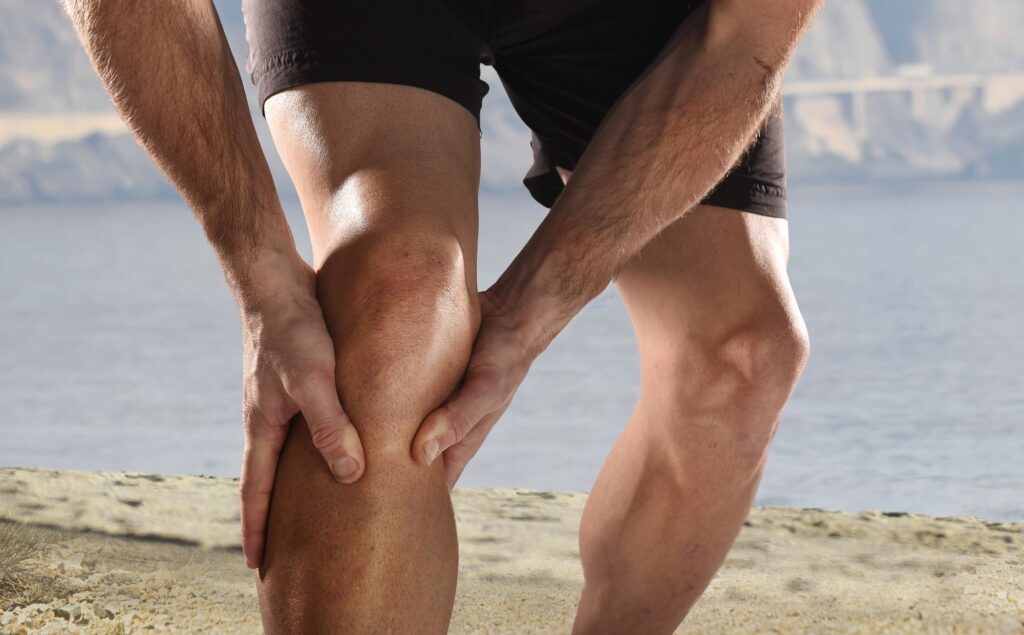
The Silent Threat: Lacerations – The Most Common Injury Caused by Unsafe Machine Operation
In the symphony of industry, a constant hum underlines the tireless work of machines. These mechanical marvels propel progress, but their power demands respect. Unfortunately, when safety protocols are neglected, a discordant note rings out – the toll of workplace injuries. Among these injuries, one reigns supreme in frequency: lacerations.
This comprehensive guide delves into the world of lacerations, the most common injury caused by working with machines unsafely. We’ll explore the gruesome details, delve into preventative measures, and answer frequently asked questions to empower you to navigate the workplace with confidence and caution.
The Gruesome Reality of Lacerations
A laceration, simply put, is a tear or cut in the skin or underlying tissue. While seemingly straightforward, the severity of lacerations can vary drastically. Minor cuts might require simple bandaging, while deep gashes can necessitate stitches or even surgery. The severity depends on factors like:
- Depth: Deeper lacerations that penetrate beyond the surface layers of skin require more extensive medical attention to close and prevent infection.
- Location: Lacerations near nerves, blood vessels, or tendons pose a greater risk of permanent damage and require specialized care.
- Object Causing Injury: Sharp, jagged objects like blades or saws can inflict more severe lacerations compared to blunt objects.
- Force of Impact: The greater the force behind the contact with the machine, the more extensive the laceration can be.
Beyond the immediate physical trauma, lacerations can have cascading consequences:
- Pain and Discomfort: The healing process is often accompanied by pain and discomfort, impacting work performance and daily life.
- Infection Risk: Open wounds are susceptible to infection, which can lead to further complications like fever, cellulitis, and even sepsis.
- Scarring: Depending on the severity, lacerations can leave permanent scars, affecting both aesthetics and functionality in some cases.
- Psychological Impact: The experience of a workplace injury can be traumatic, leading to anxiety or fear around operating machinery.
The Symphony of Unsafe Practices
Lacerations aren’t inevitable occurrences – they’re the result of a discordant orchestra of unsafe practices. Here are some common culprits:
- Lack of Training: Inadequate training on proper machine operation and safety protocols leaves workers vulnerable to accidents.
- Ignoring Safety Devices: Guards, shields, and protective gear are essential safeguards. Bypassing them significantly increases the risk of lacerations.
- Improper Use of Tools: Using tools for purposes they weren’t designed for or using them in a damaged state is a recipe for disaster.
- Distraction and Fatigue: A lapse in focus or operating machinery while tired can lead to unintended contact with sharp edges or moving parts.
- Poor Housekeeping: Cluttered workspaces or slippery surfaces can lead to slips and falls, potentially resulting in lacerations from tools or machinery.
The Harmony of Safety: Preventing Lacerations
The good news is that the risk of lacerations can be significantly reduced through a harmonious blend of preventative measures:
- Comprehensive Training: Employers have a responsibility to provide thorough training on safe machine operation, hazard identification, and proper use of personal protective equipment (PPE).
- Utilizing PPE: The right safety gear like gloves, safety glasses, and cut-resistant clothing can be the difference between a minor scrape and a serious laceration.
- Regular Maintenance: Regularly inspecting and maintaining machinery ensures all safety features are functioning correctly.
- Guarding Moving Parts: Guards and shields should never be removed or bypassed. They are essential barriers protecting operators from moving parts.
- Clear Workspaces: Maintaining a clean and organized workspace minimizes the risk of slips and falls that could lead to lacerations.
- Focus and Awareness: Workers need to be present and focused while operating machinery. Fatigue or distractions significantly increase the risk of accidents.
- Reporting Unsafe Conditions: Employees must feel empowered to report any unsafe conditions or practices to their superiors for prompt rectification.
The Importance of Reporting Lacerations
Even with the best preventative measures, accidents can happen. If you sustain a laceration while working with machinery, it’s crucial to follow these steps:
- Seek Medical Attention: The severity of the laceration will determine the necessary medical intervention. Don’t hesitate to seek immediate medical attention for serious or deep cuts.
- Report the Incident: Inform your supervisor about the accident and the circumstances surrounding it. This helps with accident investigation and prevents similar incidents in the future.
The Constant Encore: Ongoing Safety Measures
Preventing lacerations isn’t a one-time performance; it’s an ongoing safety encore. Here are some additional practices to maintain a culture of safety:
- Safety Meetings and Incentives: Regular safety meetings keep employees informed about potential hazards and reinforce safe practices. Implementing safety incentive programs can further motivate employees to prioritize safety.
- Toolbox Talks: Short, focused discussions before work shifts can address specific safety concerns relevant to the tasks at hand.
- Incident Reporting and Analysis: A robust system for reporting and analyzing workplace incidents allows for identifying trends and implementing corrective measures to prevent similar accidents in the future.
- Employee Participation: Encouraging employee participation in safety initiatives fosters a sense of ownership and accountability for maintaining a safe work environment.
- Near Miss Reporting: Even near misses where no injuries occur should be reported and investigated. This proactive approach helps identify potential hazards before they cause accidents.
- Safety Culture Leadership: Effective safety starts at the top. Company leadership needs to demonstrate a strong commitment to safety and prioritize creating a safe working environment.
Beyond Lacerations: A Holistic Approach to Workplace Safety
While lacerations are the most common injury, workplace safety encompasses a broader spectrum of potential hazards. Here are some additional considerations:
- Slips, Trips, and Falls: These seemingly innocuous incidents can lead to serious injuries like broken bones and head trauma. Maintaining a clean and organized workspace, wearing proper footwear, and being mindful of walking surfaces can significantly reduce this risk.
- Musculoskeletal Disorders (MSDs): Repetitive motions and awkward postures can lead to MSDs like carpal tunnel syndrome or back pain. Implementing proper ergonomics, taking regular breaks, and practicing safe lifting techniques can help prevent these conditions.
- Exposure to Hazardous Materials: Certain workplaces involve exposure to chemicals, dust, or fumes. Following proper safety protocols, utilizing appropriate PPE, and maintaining adequate ventilation are crucial to protect workers from these hazards.
- Fire Safety: Having a comprehensive fire safety plan in place, including fire drills and readily available fire extinguishers, is essential to ensure worker safety in case of a fire emergency.
The FAQ Symphony: Addressing Your Concerns
- Q: What should I do if I witness an unsafe practice by a coworker?
- A: Report the unsafe practice to your supervisor or safety officer immediately. It’s better to be proactive than witness an accident.
- Q: I’m worried about retaliation for reporting an unsafe condition. What can I do?
- A: Most workplaces have anonymous reporting systems in place to encourage employees to report safety concerns without fear of retaliation.
- Q: Can I refuse to operate machinery if I believe it’s unsafe?
- A: Absolutely! Workers have the right to refuse unsafe work. If you have a reasonable belief that operating the machinery poses a risk of injury, communicate your concerns and refuse to operate it until the situation is addressed.
- Q: What if my employer doesn’t provide adequate safety training or PPE?
- A: This is a serious violation of workplace safety regulations. Contact your local occupational safety and health administration (OSHA) office to report the issue.
The Final Note: A Symphony of Safety Awaits
The industrial symphony thrives on the harmonious collaboration of machines and humans. By prioritizing safety and implementing preventative measures, we can ensure the music continues without the jarring discord of lacerations and other workplace injuries. Remember, safety is not a solo performance; it’s a collective effort requiring commitment from both employers and employees. Let’s work together to create a workplace symphony where safety takes center stage, ensuring a productive and injury-free environment for all.